Human-centric innovation and skills for safety in construction
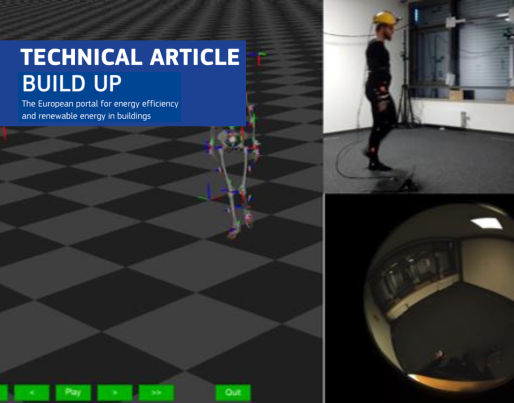
Human-centric innovation and skills for safety in construction
Explore the transformative journey of BEEYONDERS and HumanTech in the construction sector, focusing on human-centric innovation and safety. Discover how wearables, exoskeletons, and AI redefine industry standards, fostering efficiency and well-being.
Authors
Elena Maria Petrich, European Builders Confederation (EBC)
Fernando Sigchos Jiménez, European Builders Confederation (EBC)
José Carlos Jiménez Fernández, Tecnalia Research & Innovation
Markus Miezal, Sci-track
Social media profiles
(Note: opinions in the articles are of the authors only and do not necessarily reflect the opinion of the EU).
Introduction
In the context of the European Year of Skills, the European Union has been focusing on raising awareness and incentivising actions to help people get the right skills for quality jobs and to support companies in addressing skill shortages in Europe. Having a workforce with relevant skills is important not only for sustainable growth and long-term competitiveness but also to ensure that green and digital transitions are achieved. The construction sector is no exception and is in fact one of the most critical and strategic industries in this respect.
Construction represents a major slice of the European economy, representing between the 9 and 11% of the EU GDP. However, the sector faces challenges hampering its competitiveness and its path to become greener, safer, and more efficient. These include structural labour shortage, a lack of digital and green skills, little motivation of young people to join, gender-related issues, or a need to improve the safety and well-being of construction workers.
Small and medium-sized enterprises (SMEs) make up 99% of the construction sector, with
95% being micro companies with less than 10 people [1]. To meet the environmental targets set by the European Green Deal, particularly the levels of buildings energy renovation of the Renovation Wave, crafts, micro companies and SMEs in the construction sector are essential, and so is the need of up-skilling and re-skilling the construction workforce.
And here, a combination of robotisation, automation, and digitalisation could play a significant role. In this scenario, the Horizon Europe sister projects BEEYONDERS and HumanTech aim at addressing these challenges by producing human-centred technology solutions. Both projects ambition to integrate beyond the state-of-the-art innovation like exoskeletons, connected wearables, or augmented/virtual reality tools using artificial intelligence into real construction scenarios. All this, with at the same time bridging the gap between a fast-paced innovation community and a slow uptake of technology by small construction companies.
Human-centric innovation
In an era characterised by rapid technological advancements, the construction industry is undergoing a slow revolution with the integration of human-robot collaboration and wearable technologies. Both the BEEYONDERS and the HumanTech projects stand at the forefront of this transformative journey. These initiatives not only address the pressing issues of safety and efficiency in the construction sector but also highlight the potential added value that wearables and exoskeletons bring to the table.
Their approach involves the seamless integration of human and robotic capabilities to enhance overall productivity and safety, known as Human Robot Collaboration (HRC). In the construction sector, where physical demands are high and safety concerns prevalent, HRC has emerged as a game-changer. The BEEYONDERS and the HumanTech projects recognise the need for a symbiotic relationship between humans and robots to create a more productive and secure work environment.
To achieve these objectives, human-centred design [2] has been adopted. This methodology is an approach to interactive systems development that aims to make systems usable and useful by focusing on the users, their needs, and requirements, and by applying human factors/ergonomics, as well as usability knowledge and techniques. This approach enhances effectiveness and efficiency, improves human well-being, user satisfaction, accessibility, and sustainability, and counteracts possible adverse effects of use on human health, safety, and performance.
Wearables and sensors for safety in construction
Central to BEEYONDERS and one of the main objectives of HumanTech is the development of exoskeleton prototypes designed specifically for construction workers. Exoskeletons function as force multipliers, augmenting the physical capabilities of human workers and reducing the strain associated with lifting and carrying heavy loads. These wearable devices provide crucial support to the musculoskeletal system, reducing the risk of injuries and fatigue among construction workers.
Together with exoskeletons, the BEEYONDERS and the HumanTech projects emphasise the development of smart wearables to further elevate the construction industry's standards. These wearables are equipped with sensors and communication technologies, creating a connected and intelligent work environment.
One of the primary functions of these smart wearables is to monitor and enhance worker safety. Embedded sensors can indeed detect environmental hazards, such as excessive noise, temperature variations, or toxic gases, providing real-time alerts to workers and supervisors. This initiative-taking approach to safety could ensure a quicker response to potential risks, preventing accidents and injuries on the construction site. Regarding the integration of smart wearables for construction workers, BEEYONDERS, for example, focuses on the manufacturing and implementation of a suite of wearable sensors that will be applied to worker's clothes or personal protective equipment to monitor the well-being of the workers through the different tasks executed throughout a working day. To evaluate any risk for the workers, environmental parameters will be measured and combined with risky behaviour of physical parameters such as the workers’ activity recognition through accelerometers, location on the worksite through GPS or ergonomics evaluation.
An IoT framework will provide a continuous stream of data from the wearable sensors to the Digital Twin that will allow the collecting of relevant information to improve users’ safety, by providing real time alerts when any risky situation can arise. AI algorithms will then analyse the collected data to extract patterns that could potentially indicate a high risk for injuries and inform the workers in a preventive action. Although this might sound futuristic, investing such a scenario could lead to pioneering progress.
The integration of wearables and exoskeleton in the construction sector through these Horizon Europe offers several tangible benefits, adding significant value to the workforce. The first benefit identified is the improvement of the safety culture, due to real-time monitoring capabilities of smart wearables and exoskeleton that contribute to the development of a safety-first culture on construction sites. By providing instant alerts and preventive measures, these human devices mitigate potential hazards, fostering a secure working environment. This approach will be tested and validated at the projects’ use cases focusing on building and construction environments. Despite the initial investment in developing and implementing these technologies, the long-term benefits include reduced worker risks, increased efficiency, and minimised project delays. The overall cost-effectiveness of the technology contributes thus to the sustainability and competitiveness of construction projects.
In a nutshell, the BEEYONDERS and HumanTech projects’ focus on HRC, and the development of wearables signifies a groundbreaking approach to revolutionise the construction industry. By addressing safety concerns, enhancing productivity, and fostering a culture of innovation, these initiatives set the stage for a new era in construction. As the prototypes of exoskeletons and smart wearables become integral components of construction sites, the added value they bring to the sector becomes increasingly evident, marking a significant step towards a safer, more efficient, and technologically advanced construction industry.
Figure 1. StreamEXO is the background technology used in Beeyonders for exoskeletons, and it has been awarded with the IF-Design Award.
User acceptance and customisation
The integration of exoskeletons in construction not only enhances the strength and endurance of workers but also allows for more precise and controlled movements. This increased precision is particularly valuable in tasks that require fine motor skills, contributing to improved overall efficiency and quality of work.
However, if on the one hand exoskeletons have great potential to reduce the load of physical work such as heavy lifting, on the other hand they need further developments and adaptions to fit the morphological needs and mental considerations of construction workers. Indeed, although the potential to improve biomechanical loading support and avoid musculoskeletal injuries seems promising, curiosity first then acceptance by the current construction workforce remain challenging.
Today’s construction workers might feel monitored, restricted in their movements, or stressed by an information overload, while different human typologies and gender considerations could require further customisation. An additional drawback when thinking of exoskeletons is that they impede natural motion when, for example, the worker must climb stairs or ladders or drive a forklift. In those cases, the worker needs to switch off the exoskeleton, and then switch it on again to perform the physical work, which is a bothersome situation and leads to a lack of acceptance.
For these reasons, in both projects, user acceptance is one of the key factors to design technologies that are impactful but at the same time likely to be endorsed by the construction workforce of today and tomorrow. For example, the HumanTech project pursues a concept called ‘intelligent transparency’ to recognise the intention of the user and the physical context to activate or deactivate the supporting functionality of the exoskeleton. The aim is to aid on an ‘as needed’ basis. For this reason, one key source of information to better shape and develop the control of the exoskeleton by workers consists of a body-worn visual/inertial sensor network. With time, inertial sensors have become smaller, lighter, and more easily integrated into comfortable market-ready solutions which make their deployment for industrial applications feasible.
A common application for these inertial sensors, which measure acceleration including gravity, rotational velocity, and the magnetic field, is orientation estimation. Despite their versatility, it lacks a widespread usage in industrial applications due to open issues like acceleration biases and magnetic disturbances. Ferromagnetic materials or metal structures influence the local magnetic field, so that, particularly with sensor networks, different yaw references are present among the sensors.
In lab environments though, this technology has already been successfully applied on industrial workers e.g. ergonomic assessment, or on a low level for exoskeleton control. For the latter, if, for example, an exoskeleton is designed to support overhead work, but the person is instead bending forward and reaching, the direction of gravity, i.e. the person's orientation, is important to determine if support is required.
Figure 2: The HumanTech sensor network can be comfortably worn below work clothing and protective equipment.
In contrast to this, the HumanTech approach aims for the more complex goal to detect the workers intention which allows determine the mode and requirement of support beyond pure posture. To add more context, a dual-fisheye camera is mounted on the helmet of the worker. The wide field of view offers multiple benefits. Primarily, the information will be used to localise the worker inside a BIM model, which supports the intention prediction. But the worker himself is visible in the camera view. By detecting the body posture or joint positions in the image and fusing this with the inertial tracking, intrinsic and extrinsic drift can be avoided, and the above-mentioned failure-prone magnetic measurements can be omitted completely.
Figure 3: HumanTech tracking example from the visual/inertial sensor network. Here, markers serve as anchor to the BIM model.
Beyond this, the positional information puts the executed work in the spatial-temporal context of the construction site. In combination with virtual reality or augmented reality headsets, related IFC objects can be linked to the current task. This allows for progress monitoring of the whole construction site, but also issue management and (visual) documentation can be performed on-site in a paperless manner. This simplifies and speeds up processes. In the same way that workers interact with a BIM model, objects like tools or robots can also be managed within an extended BIM model. On the long-term robot maintenance, control or interaction may be able for the digital worker, to help both productivity, safety, and well-being.
In addition to assessing the degree of acceptance on the part of construction workers, specific training modules and activities must be provided to upskill and reskill the current workforce. For this reason, the following section aims to briefly explain what the two projects are doing in terms of developing training schemes.
Training schemes
The construction sector is one of the least digitalised [3], and one struggling to attract young people, women, or migrant talent [4]. The technologies that HumanTech and BEEYONDERS are developing envision a harmonious co-existence with human workers, to attract new workforce thanks to innovative approaches to training.
Such training schemes could involve streaming of collected data, as well as automatic expert knowledge capturing with wearable cameras in the form of workflows, which could then be conveyed to the new talent with the use of augmented reality tools. A combination of virtual case studies, gamification, or videos could enable workers to upskill as part of formal on-site training or as a progressional training plan.
To improve the fidelity of the serious game learning simulations and provide the participants with the most suitable realistic experience during the training, a specific part of the work is set on realising the next generation level of active learning by integrating body motion sensors, hand tracking, realistic representation of avatars during gameplay, and forced feedback with the use of the exoskeleton.
However, a critical aspect of these training initiatives is to strike a balance between digital advancement and preserving a sense of danger. The immersive nature of these simulations should not desensitise workers or apprentices to real-world risks. Striving for a gender-neutral and appealing environment, these technology-assisted courses contribute to making construction not only safer and greener but also more enticing to a diverse and dynamic workforce.
Conclusions
In conclusion, BEEYONDERS and HumanTech signal a transformative phase in construction, emphasising human-centric innovation for enhanced safety and productivity. The integration of wearables and exoskeletons marks a paradigm shift, fostering a robust safety culture, reducing risks, and amplifying efficiency. Prioritising user acceptance and customisation, these technologies redefine work dynamics. Simultaneously, recognising the critical role of workforce skills in sustainable growth, these initiatives address the construction sector's unique challenges: the prevalence of micro and small enterprises, an ageing workforce, and the imperative to attract younger talent. As SMEs embark on their digitisation path, BEEYONDERS and HumanTech pioneer disruptive technologies and innovative training models. This dual commitment ensures a safer, greener, and more appealing future for construction, grounded in the central role of human knowledge and expertise, making the industry resilient and attractive to new talents and diverse demographics.
References
[1] EUROPEAN COMMISSION Directorate-General for Internal Market, Industry, Entrepreneurship and SMEs Directorate H – Ecosystems III: Construction, machinery & standardization, Transition Pathway for Construction
[2]The term “human-centred design” is used rather than “user-centred design” to emphasize that the part of ISO 9241 also addresses impacts on a number of stakeholders, not just those typically considered as users. However, in practice, these terms are often used synonymously. (Source: ISO 9241-210:2010).
[3] European Commission, Executive Agency for Small and Medium-sized Enterprises, ‘Supporting digitalisation of the construction sector and SMEs – Including building information modelling’, Publications Office of the European Union, 2019, https://data.europa.eu/doi/10.2826/422658
[4] European Commission, European Labour Authority, EURES Report on labour shortages and surpluses 2022, https://www.ela.europa.eu/sites/default/files/2023-09/ELA-eures-shortages-surpluses-report-2022.pdf