
Integrating human-centric design with emerging technologies in construction
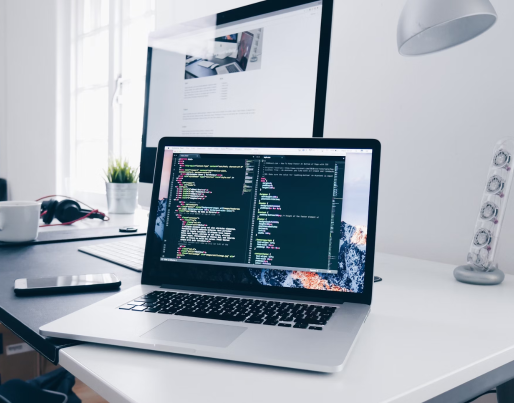
Integrating human-centric design with emerging technologies in construction
Integrating human-centric design with BIM, IoT, Digital Twins, and additive manufacturing marks a transformative era in construction, enhancing efficiency, sustainability, and adaptability. The fusion of these technologies with human expertise redefines building design, construction, and management, despite challenges in data management and interoperability. The digital revolution reshapes the construction value chain, demanding a shift in industry roles, responsibilities, and a focus on continuous innovation and collaboration.
Authors
Luis de Pedro, Infrastructure Director at NTT DATA
LinkedIn profile
Jorge Luis Manzoni, Expert Sector Consultant | Infrastructure, Services & Real Estate at NTT DATA
LinkedIn profile
Luis Margarito Lira Aponte, Senior Sector Consultant | Hospitality & Logistics at NTT DATA
LinkedIn profile
(Note: opinions in the articles are of the authors only and do not necessarily reflect the opinion of the EU).
Introduction
The construction industry is at the cusp of a digital revolution, marked by the combination of advanced technologies such as Building Information Modelling (BIM), the Internet of Things (IoT), Digital Twins, and additive manufacturing [1]. These improvements are not only transforming the way buildings and other types of facilities are designed, constructed, and managed but also redefining the relations between human activities and technology. The synergy between these digital tools and human expertise is adopting a new era of decision-making in construction processes, characterised by enhanced efficiency, sustainability, and adaptability to changing needs.
BIM serves as the foundation, providing a 3D digital representation of physical and functional characteristics of building elements, thereby facilitating collaboration among various stakeholders throughout the building lifecycle. IoT extends this capability by integrating real-time data from the physical environment, enabling dynamic updates and interactions within BIM models. Digital Twins further advance this integration by mirroring the physical built environment in a digital platform, allowing for real-time monitoring, simulation, and control. Additive manufacturing introduces a new dimension of construction by enabling the fabrication of complex building components directly from digital models, promising customisation, and efficiency.
However, the digital transformation of the built environment is not without challenges. Issues such as data management, interoperability, and the integration of these technologies into existing workflows pose significant hurdles [1]. Moreover, the human-centric aspect of construction, (emphasising user experience, collaborative decision-making, and adaptive design) remains paramount amidst the adoption of these technologies.
Revolutionising construction collaboration
Building Information Modelling (BIM) is at the forefront of transforming project management within the construction industry, enhancing collaboration, accuracy, and cost efficiency significantly [2]. By providing detailed geometric information coupled with various simulations, such as energy and thermal environment simulations, BIM facilitates optimised design of buildings and their systems. This not only aids in refining construction processes but also in streamlining management plans, leading to a more efficient project execution. All these can be handled using integrated 5D Platforms that allows companies in the AEC sector to optimise the use of the BIM model.
The integration of Digital Twin (DT) technology with BIM is rapidly transforming the construction sector by offering a virtual counterpart of physical assets, processes, and systems [3]. This combination plays a pivotal role in optimising construction planning and management processes. By simulating various design scenarios, construction managers can evaluate impacts on project timelines and costs, and identify potential issues before the actual construction begins, minimising delays and enhancing project outcomes. This is possible by collecting data from previous projects or infrastructure that are already in service.
For instance, a framework that utilises high-fidelity DT to provide real-time information on resource status and construction progress facilitates planning, scheduling, and execution processes in construction projects [3]. DT technology also fosters collaboration and communication among stakeholders, including architects, engineers, contractors, and clients, by providing a shared virtual environment. This environment allows for the visualisation of the project, discussion of design alternatives, and making informed decisions, thereby enhancing the efficiency of project management.
BIM serves as a reliable approach for sustainable construction (BIM 6D), dividing related studies into environmental, economic, and social dimensions [2]. The technology is instrumental in the energy efficiency of building structural systems, underscoring the necessity of BIM in future sustainable decision-making. During the building operation stages, BIM's advanced data storage capability and vivid representation of building information proves invaluable. This facilitates a comprehensive review of the status quo of BIM applications in building operation and maintenance, highlighting the technology's potential to improve efficiency in building design, construction, and operation phases.
Practical use of BIM has gained importance, enabling easy access to building plans via digital devices and real-time monitoring of building progress [2]. This breaks down barriers between previously siloed activities, providing better integrated and flexible design and build stage processes. The potential of BIM in enhancing safety through automated identification and prevention of construction worker fall hazards on-site is notable. Such systems can serve as a real-time automated hazard checker, underlining the importance of BIM as part of standard safety planning processes for construction projects.
The backbone of smart construction sites
The Internet of Things (IoT) plays a pivotal role in transforming construction sites into hubs of real-time monitoring and operational efficiency. By deploying a network of sensors across construction sites, IoT provides a continuous stream of data, complementing BIM's detailed datasets. This synergy offers a holistic view of the construction project, enhancing both safety and project management practices. As was mentioned before, data could come primarily from projects under construction or infrastructure already on service.
IoT devices, integrated with BIM, can capture real-time data including project status, construction activities, and physical context. This information is crucial for updating construction schedules and ensuring quality control.
The integration of IoT with BIM goes beyond mere data collection. It encompasses health and safety management by monitoring environmental and human activities associated with risks on construction sites [4]. This integration is particularly useful for continuous improvement, compliance, and insurance optimisation. Advanced applications include H&S training systems that utilise BIM and sensor technology to track the location of personnel and equipment during training, thereby enhancing safety and productivity through real-time and post-event visualization in a VR environment.
Mirroring the future of infrastructure
Digital Twins represent a significant leap forward in infrastructure management, embodying the synergy between the virtual and physical realms [5]3. This integration enables dynamic management of infrastructures, facilitating predictive maintenance and informed decision-making by mirroring the real world with a virtual model. The essence of Digital Twins lies in their ability to provide real-time visualisation and prediction, supporting automatic feedback and control of the built environment. With intelligent feedback control systems, Digital Twins allow the built environment to automatically respond based on optimised results and control strategies, typically leveraging AI algorithms for seamless interaction between the virtual and real-world environments.
At the core of Digital Twins is the capacity to visualise real-time data from the built environment, such as construction progress, indoor conditions, and occupant dynamics [5]. This real-time insight enables predictive decision-making based on dynamic building information, paired with data sensing. Automatic control feedback mechanisms with optimised management strategies allow for interventions in the built environment, enhancing operational efficiency and sustainability.
Despite the promise, the adoption of Digital Twins in construction faces challenges, such as the design of processes, manual data conversion, and reliability of sensor-collected data. Current research often focuses on single-use cases, underscoring the need for a more integrated framework that consolidates data from various sensors to fully realise the concept of smart construction sites.
Managing the vast amounts of data generated by these technologies and ensuring efficient information exchange remains a formidable challenge. Integration methods and the need for standardised data formats are critical for overcoming interoperability issues and enabling seamless collaboration among stakeholders.
Integrating technology with a focus on user-centric design is crucial. Digital Twins, for instance, not only provide technical insights but also offer opportunities to enhance the user experience by simulating real-world scenarios and responses within the built environment.
Digital Twins provide a great benefit to BIM models, since they do not have to collect all the data in the native format, the Digital Twin can consult different Databases of the 3D model, without expanding the capacity of the file.
The impact of digital technologies on the construction value chain is profound, reshaping traditional practices and workflows. The adoption of these technologies demands a re-evaluation of roles, responsibilities, and skills within the industry, highlighting the need for continuous learning and adaptation.
Conclusions
The integration of emerging technologies such as BIM, IoT, Digital Twins, and additive manufacturing is marking the beginning of a transformative era in the construction industry, characterised by increased efficiency, sustainability, and adaptability to human needs. However, effectively managing the vast volumes of data generated by these technologies and ensuring efficient information exchange present significant challenges that require meticulous attention.
Effective data integration and information exchange are crucial to overcoming interoperability issues and fostering seamless collaboration among stakeholders. Implementing integration methods and adopting standardised data formats are essential to navigate the complex data landscape and ensure harmonisation across the various platforms and tools used in construction projects.
Adopting a user-centred design approach is crucial in technology integration. Tools like Digital Twins not only provide technical insights but also enhance the user experience by simulating real-world scenarios and responses within the built environment. This approach ensures that technological solutions are not only technically advanced but also intuitive and satisfying for end-users.
The impact of digital technologies on the construction value chain is profound, reshaping traditional practices and workflows. The adoption of these technologies necessitates a re-evaluation of roles, responsibilities, and skills within the industry, highlighting the need for continuous learning and adaptation. This transformation is not only technological but also cultural, requiring a shift in mindset among construction professionals toward innovation, collaboration, and continuous improvement.
References
[1] Sawhney, A., Riley, M., & Irizarry, J. (Eds.). (2020). Construction 4.0: An Innovation Platform for the Built Environment. Routledge.
[2] Eastman, C., Teicholz, P., Sacks, R., & Liston, K. (2011). BIM Handbook: A Guide to Building Information Modeling for Owners, Managers, Designers, Engineers, and Contractors. John Wiley & Sons.
[3] Tang, S., et al. (2019). The integration of BIM and IoT: A systematic review. Automation in Construction, 101, 127-139. DOI: 10.1016/j.autcon.2019.01.020.
[4] Gan, V. J. L., et al. (2019). The need for comprehensive validation protocols to standardize health and safety management: A systematic review. Automation in Construction, 104, 77-91. DOI: 10.1016/j.autcon.2019.04.005.
[5] Lu, Q., et al. (2020). From BIM to Digital Twins: Integrated BIM and IoT—A Systematic Review. Buildings, 10(4), 62. DOI: 10.3390/buildings10040062.