
Measuring and reducing embodied carbon in the building envelope
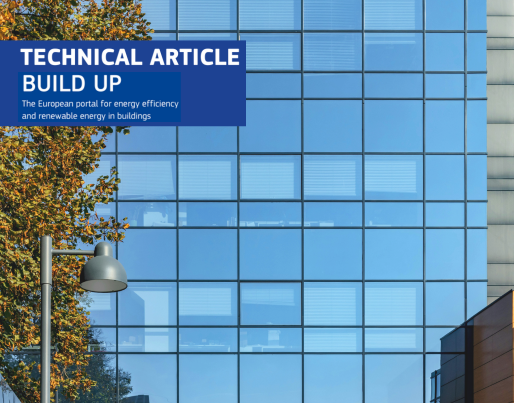
Measuring and reducing embodied carbon in the building envelope
Two case studies of office buildings in Bologna, Italy, benchmark cradle-to-gate upfront carbon emissions of curtain walling. Despite data uncertainties, guidance from the Centre for Window and Cladding Technology (CWCT) aids in managing embodied carbon in aluminium profiles and glazing. This study demonstrates that the choice of low-carbon materials can reduce façade emissions by up to 30%.
Authors
Marco Capelli, Facade Engineer, BECxA, LEED AP BD+C, Open Project | LinkedIn
Andrea Botti, Head of Sustainability, Open Project | LinkedIn
Alice Garoni, Façade Engineer, BIM Specialist, Open Project | LinkedIn
Francesco Conserva, Vice President, Open Project | LinkedIn
(Note: opinions in the articles are of the authors only and do not necessarily reflect the opinion of the EU).
Introduction
Open Project's previous research confirmed that structures are the largest contributors to building CO2 emissions, but the building envelope can contribute up to 20%. As progress is made in reducing structural emissions, addressing the Global Warming Potential (GWP) of the building envelope will become increasingly significant, particularly during recladding work on existing buildings [1]. Open Project’s assessment indicates the embodied carbon of the building envelope ranges from 72 to 183 kg CO2e/m² Façade Surface Area (FSA) for The Social Hub and Unahotels Bologna Fiera respectively, the latter having higher emissions due to aluminium composite panels and extruded profiles [2].
High-performance building envelopes are crucial for minimising operational carbon emissions and enhancing indoor environmental quality. While good visible light transmission glazing can reduce reliance on artificial lighting, solar control glazing can reduce HVAC loads and operational energy usage, but possibly increase embodied carbon when external solar shading is implemented.
Replacing the building envelope is a key strategy to extend the service life of existing buildings and reduce CO2 emissions. The strategies of ‘Transform and Reuse’ and ‘Build less’, are indicated by LETI (London Energy Transformation Initiative) as the most effective for reducing upfront carbon emissions. When a new envelope is necessary, the ‘Build clever’ strategy offers significant potential for reducing upfront carbon emissions by optimising façade modules and choosing low-carbon glass compositions. The ‘Build low carbon’ strategy involves specifying materials (aluminium and glass) with high recycled content and low carbon manufacturing processes, including the minimisation of waste by using post-consumer glass cullet for glass.
Open Project aims to investigate the embodied carbon of building envelopes, its significance in overall building carbon, and the data and guidelines for its estimation. The goal is to define a benchmark for cradle-to-gate CO2 emissions of curtain walling systems in office buildings, focusing on two buildings in Bologna, Italy; one completed and occupied and one yet to be constructed. The study primarily examines the upfront CO2 emissions of glazed curtain walling, which is common in office buildings, comparing façade sections of similar performance. The research also evaluates the availability and reliability of data for estimating embodied carbon in aluminium extruded profiles and glass.
Open Project case studies
Two recent Open Project high performance buildings have then been chosen as case studies. Prometeia HQ is LEED Gold certified and Tecnopolo F2 is registered for LEED certification.
The quantities and type of aluminium extruded profiles and TGG have been calculated and used as input for LCA calculations.
Prometeia HQ
Prometeia is an international consultancy company and chose an existing 1980s office building as their new HQ in Bologna, Italy. Open Project was responsible for the Scheme Design and Detailed Design (2017-2018) on behalf of the owner. The building was completed and occupied in 2019.
Figure 1 Prometeia HQ, North Façade
The existing structure has been retained, with minor seismic improvement only (thus minimising the upfront carbon emissions) with a full recladding and fit out. The North Façade comprises a TGU SSG unitised system (typical unit size is 2400mm x 3700mm), with parallel projecting windows.
Tecnopolo F2 Office Building
The Tecnopolo Bologna has been developed by Regione Emilia Romagna within the framework of the 2007-2013 European Fund for Regional Development in order to create an infrastructure for innovation, research and technology transfer within a previously developed historic preservation district, formerly known as Manifattura Tabacchi.
An international masterplan competition was held with the ECMWF (European Centre for Medium-Range Weather Forecasts) and CINECA Leonardo supercomputers, and the development is currently in progress. The Schematic Design of the Tecnopolo F2 Office Building (2012-2020) was developed by Von Gerkan, Marg und Partner gmp GmbH.
Open Project developed the Detailed Design and BIM model of the facades on behalf of the general contractor between 2022-2023 and practical completion is expected in 2025.
The north facade, used as a benchmark for the research, is a TGU stick system, with one operable full height projecting window and a glazed parapet per module, aluminium vertical feature profiles, and travertine feature columns.
Figure 2 Tecnopolo F2, North Façade. 3D View from gmp. Right: screenshot from Open Project BIM Model.
Scope of the Life Cycle Assessment
In this research a full LCA has not been done but only stages A1-A3 (cradle to gate) have been considered. For curtain walling, A1-A3 stages represent the biggest part of the Upfront Embodied Carbon, therefore the vast majority of the total emissions during the entire lifecycle.
Material quantities
The quantities of the aluminium profiles have been determined from drawings and specifications produced at the technical design stage (Stage 4).
For Tecnopolo Building F2 it was calculated that the north façade, for levels 1, 2 and 3, corresponds to a total façade area of 515 m2, and to approximately 11.345 kg of extruded aluminium profiles (approx. 22 kg / m2 FSA). GWP data was derived from project specific dynamic EPDs provided by the aluminium system supplier Schuco, who was appointed by the general contractor.
For Prometeia HQ it was calculated that the north façade for levels 1 to 5 has a total façade area of 1570 m2, corresponding to approximately 11.217 kg of extruded aluminium profiles (approx. 7 kg / m2 FSA).
Embodied carbon data for glazing systems
A variety of data sources have been taken into consideration for this study:
The study ‘Carbon footprint of façades: significance of glass’ by Arup & Saint Gobain Glass [3] examined the variability in embodied carbon across different façade designs, considering various typologies, materials, and design factors, and revealed significant differences in the overall embodied carbon of facades based on the typology employed. Furthermore, the study assessed the embodied carbon of unitised curtain wall systems and their impact on a building's operational demand, looking at the influence of different design and material choices. The focus was on unitised curtain wall façade systems due to their prevalent usage in residential and commercial properties in the UK and Europe.
The Centre for Window and Cladding Technology (CWCT) ‘How to calculate the embodied carbon of facades: a methodology’ [4] and worked example [5] (in Appendix C) provide useful and reliable data for conducting preliminary estimates of CO2 emissions of glazing systems. It is worth noting that material quantities (thickness, density, weight) are not the only required data to produce carbon estimates, and thermal processing, such as tempering or heat strengthening, as well as other processes like coating, laminating, assembling in DGU or TGU have a documented impact on the embodied carbon, which this guidance helps to quantify.While it is understood that estimations in line with CWCT can include margins of error of 10-15%, this method is valuable for preliminary estimates at early design stages.
Online glazing configurator tools made available by glazing manufacturers often integrate embodied carbon data from EPDs. These tools can provide accurate data to be used for embodied carbon calculations during the Detailed Design stage. This is preferable than using the glass manufacturer’s EPDs for clear float glass or coated float glass, since they do not consider the glass processing required for high performance glazing systems, or EPDs for DGUs or TGUs, since they often refer to simple compositions typically used in the residential market, and they do not consider the increased glass panes thickness and processing required for office buildings high performance glazing.
Embodied carbon data for extruded aluminium profiles
The available data for aluminium extruded profiles do not offer the same level of accuracy and reliability as it does for glazing because of the high variation between different manufacturers and an even greater variability between different geographic areas. The recycled content, which is the main driver for the CO2 emissions reduction in aluminium cullet manufacturing, is not always clearly specified in EPDs. Thus, the literature on CO2 emissions varies from 6.83 kgCO2e / kg (database ICE European average [6], based on 31% world average recycled content) to 10.25 kgCO2e / kg (Aluminium Extruders Council, North America average, with 50% pre-consumer and 19% post-consumer recycled content).
Primary European aluminium façade and windows off the shelf systems, such as Wicona Hydro and Schuco, can provide the façade engineer with project specific EPDs, that typically include other components such as thermal breaks, gaskets, accessories, brackets, etc.
Figures between 3.30-4.80 kgCO2e / kg aluminium (including the contribution of thermal breaks, gaskets, accessories, etc. but excluding the contribution of glazing) have been obtained from the EPDs of stick system façade systems. Therefore, the CO2 emissions declared by the primary European manufacturers are much smaller than the European average as per the ICE database. This is due to a constantly increasing use of recycled content in the aluminium ingots (42% for Schuco, 75% for Hydro Circal) and the use of renewables for aluminium ingots production and extrusion. Further reductions are expected soon.
Preliminary estimates for early-stage design phases
Since ‘Build Clever’ is the strategy with the highest potential for reducing upfront carbon emissions under the stewardship of the architect and façade engineer, the data already demonstrates that the north façade of Prometeia HQ would have resulted in lower upfront carbon emissions compared to the Tecnopolo F2, had they been constructed using the same aluminium profiles manufacturer and the same type of glass.
The study does not delve further into the trade-off between the weight of aluminium and glass, it is useful to highlight how in very broad terms, larger sizes of glazing panes usually require less aluminium frame elements (mullions and transoms) and yet requires an increase in the thickness of the glazing.
Figure 3 Left: Prometeia HQ, North Facade. Right: Tecnopolo F2 Office Building, North Façade
In the preliminary estimate only aluminium and glass were accounted for, as these are recognised as the most prominent and impacting components of facade systems from an embodied carbon perspective. This is due both to the quantitative predominance (in terms of kg material/m2 FCA) and to their energy-intensive manufacturing processes. Other components like thermal breaks, gaskets, accessories, and brackets were not included in this estimate, though they should be accounted for in a detailed embodied carbon analysis for a facade system.
For aluminium, the estimate relied on the average European aluminium extruded profiles' GWP sourced from the ICE Database. For insulated double glazing units, calculations were conducted following the guidance from CWCT - Appendix C, considering factors such as the float glass type (low iron or mid iron), the glass thickness, any thermal processing, as well as other processes like coating, laminating, assembling in DGU or TGU.
The research can only compare the results of an estimate based on the following available reference data for preliminary estimates:
the average European aluminium extruded profiles GWP, from ICE Database [5], 6.83 kgCO2e/kg
with reference to the glass, an Open Project calculation based on CWCT Appendix C [3], resulting in 121 to 123 kg CO2e/m2 (depending on the glass thickness).
The following figures do not correspond to the overall CO2 emissions of the curtain walling, that should also include other components such as thermal breaks, gaskets, accessories, brackets, etc.) but they do represent the biggest part.
Table 1 Comparison of preliminary estimates for Prometeia HQ and Tecnopolo F2 façades
Low-carbon design scenarios: the impact of material specifications
For the façade of the Tecnopolo F2 Building, three additional scenarios were devised as low carbon improvements from the preliminary estimates representing the baseline (or Scenario 0), using the same material quantities as per Design Specifications:
Design Option / Scenario 1, corresponding to the Detailed Design Specifications, thus without any low carbon glazing or aluminium (but with a more detailed estimate using data from Saint-Gobain configurator and project specific Schuco EPDs).
Design Option / Scenario 2, same glazing as per the Design Specifications and low-carbon aluminium profiles.
Design Option / Scenario 3, low-carbon glass and low-carbon aluminium profiles.
Table 2 Comparison of preliminary estimates and alternative scenarios for Tecnopolo F2 façade.
Impact of glazing
One of the key findings is that the contribution to upfront carbon emissions (A1-A3) from glazing is greater than that associated with aluminium profiles, even when low-carbon glass is considered. This increases further when low-carbon aluminium is considered. When low-carbon options are considered for both aluminium and glazing, the latter reached 60% of the total.
Reductions via low-carbon material specifications
In the event of incorporating both low-carbon aluminium and low-carbon glass for the Tecnopolo F2 North Façade, there's potential for a further reduction of -30% (resulting in 163 kgCO2e/m2 FSA compared to the initial 244 kgCO2e/m2 FSA), representing a substantial -40% decrease from the preliminary estimates. While this reduction is notably smaller in scale compared to potential reductions in the building's structural Global Warming Potential (GWP), it remains a significant factor, especially when considering alternatives such as wood, low-carbon concrete, and steel for structural elements, or when maintaining existing building structures.
Critical review of available embodied carbon data
The next step of the research has been to get a better understanding of the reliability of the above-mentioned available source data by comparing the GWP potential by production unit (kg of extruded aluminium profile and m2 of double or triple glazed unit).
The following table shows a comparison of A1-A3 carbon emission estimates for a triple glazed unit.
Table 3 Cradle-to-gate (A1-A3) carbon emission estimates for triple-glazed unit
CWCT Appendix 2 provides figures for preliminary estimates and the results from online glazing configurator allows for more detailed estimates and allows architects and façade engineers to compare reliable embodied carbon data for different glazing products or different strategies.
For instance, architects and facade engineers may use a glazing configurator to evaluate if, from a CO2 reduction perspective, it may be preferable to use low iron glazing (without any thermal processing) or mid iron toughened or heat strengthened glass to withstand the thermal shock stress.
Primary European aluminium façade and windows off the shelf systems (such as Wicona Hydro and Schuco) can provide the façade engineer with project specific EPDs, that typically include other components such as thermal breaks, gaskets, accessories, brackets, etc.).
Furthermore, the data reveals that deriving carbon intensity using Environmental Product Declarations (EPDs) for the products defined in the design specifications determine only a very moderate reduction (-10%) from initial (baseline) estimates, which were made with generic data. This confirms that the accuracy of the preliminary estimates is acceptable.
Uncertainty when expressing embodied carbon estimates at the design stage
It is quite common to see an exact figure (say, 132 kgCO2e/m2FSA), for façade GWP in architect or façade engineer publications, but this research shows that uncertainties in the source data can significantly affect the results, and it may be recommended to declare such an exact figure together with the condition under which this has been calculated and the source data. For instance, have the aluminium CO2 emissions per FSA unit been calculated by using the average European data (preliminary estimate) or do they correspond to the actual supply chain of the as built façade and have been calculated from project specific EPDs? This appears to be in line with the statement from CWCT guidance Introduction: “(...) At this time, the following items anticipated as future work include: … Reference facade specific embodied carbon factors from open-source databases (…)”
Hopefully institutions such as SFE, CWCT or the national Green Building Councils will start to standardise the way data sources and output are presented, and to collect and share case studies results.
Conclusions
This study identifies ‘Build Clever’ as the key strategy to reduce façade embodied carbon, demonstrated by Prometeia HQ's design which minimises the use of aluminium through a choice of wider curtain wall modules and fewer openings. The ‘Build Low Carbon’ strategy further reduces GWP with low carbon aluminium and glass. Reliable data for preliminary estimates, especially for aluminium extrusions, is crucial.
The study calls for a common language for comparing façade projects and recommends contingency factors for carbon emission figures. CWCT's future work will include more specific guidance for selecting embodied carbon factors during early design stages. Project-specific EPDs are essential for accurate GWP estimates.
References
[1] WorldGBC, 2019. Bringing embodied carbon upfront. London, Sep. 2019. Available: https://worldgbc.org/advancing-net-zero/embodied-carbon/
[2] Open Project, 2023. Measuring and reducing embodied carbon in buildings: 5 hospitality case studies in Bologna, Italy. Online. Available: https://build-up.ec.europa.eu/en/resources-and-tools/articles/measuring-and-reducing-embodied-carbon-buildings-5-hospitality-case
[3] Arup, 2022. Carbon footprint of façades: significance of glass. Online. Available : https://www.arup.com/perspectives/publications/research/section/carbon-footprint-of-facades-significance-of-glass
[4] CWCT Centre For Window and Cladding Technology, 2022. How to calculate the embodied carbon of facades: A methodology, Issue 1. Available: https://www.cwct.co.uk/pages/embodied-carbon-methodology-for-facades
[5] CWCT Centre For Window and Cladding Technology, 2023. How to calculate the embodied carbon of facades: Worked example, Issue 1 Rev 01. . Available: https://www.cwct.co.uk/pages/embodied-carbon-methodology-for-facades
[6] The Inventory of Carbon and Energy (also known as the ICE database) v3.0. Online Available: https://circularecology.com/embodied-carbon-footprint-database.html