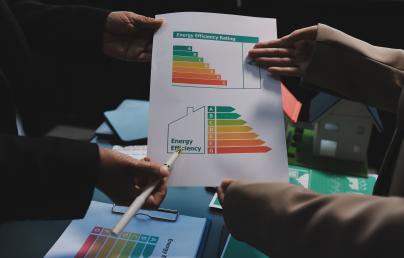
Panel insulation technology for more efficient building renovation
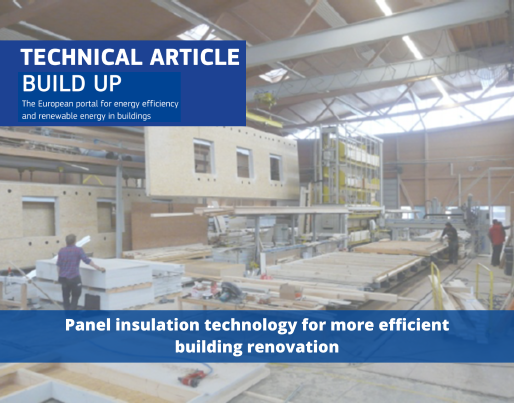
Panel insulation technology for more efficient building renovation
As renovation rates remain low across most of Europe, engineers are seeking more convenient and efficient methods to enhance the energy efficiency of buildings. This article explores a modern renovation method that uses prefabricated panels to insulate a building’s envelope more effectively, helping to save energy and reduce heating costs.
Authors
Jurgita Černeckienė, Faculty of Civil Engineering and Architecture, Kaunas University of Technology | LinkedIn profile
Darius Pupeikis, Faculty of Civil Engineering and Architecture, Kaunas University of Technology | LinkedIn profile
Vytautas Bocullo, Faculty of Civil Engineering and Architecture, Kaunas University of Technology | LinkedIn profile
(Note: opinions in the articles are of the authors only and do not necessarily reflect the opinion of the EU).
Introduction
In most EU countries, the common goal of decarbonising new construction and renovated buildings includes reducing both embodied and operational carbon dioxide emissions. In some countries, accelerating the renovation of multi-apartment buildings aligns with national goals for energy efficiency and climate action while also meeting residents’ expectations for more efficient and visually appealing upgrades to their homes. Also, the construction sector is aiming to improve efficiency through increased digitisation, achieved by implementing BIM (Building Information Modelling) concept to the whole life cycle of the buildings. Considering the sectoral trends and the current level of technological readiness, the project ‘Multi-country support to advance building decarbonisation (TSIC-RoC-19044)’ was launched. The Lithuanian team focused on promoting renovation by developing technical materials to familiarise stakeholders with panel renovation technology, using factory-produced panels made from plant-based organic materials. The project was funded by the European Union via the Technical Support Instrument, managed by the European Commission Directorate General for Structural Reform Support.
Panel insulation technology overview
Panel insulation (also known as panel renovation or insulating panels) is one of the latest technologies for enhancing the thermal performance of building envelopes. It offers high-quality results, faster on-site work processes, potential expansion of existing spaces, the introduction of new engineering systems (usually mechanical ventilation), and a competitive price for renovation.
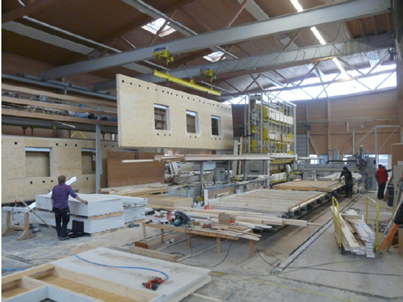
Figure 1: Wall panel fabrication in the factory (photo of E2ReBuild project)
The primary objectives of panel renovation technology align directly with EU's decarbonisation policy for buildings1 :
speeding up the renovation of multi-family housing to reduce buildings’ operational carbon footprint.
Introducing a renovation technology for multi-apartment dwellings that produces a lower embodied carbon footprint compared to traditional insulation and renovation technologies.
The first objective focuses on achieving faster and more efficient panel refurbishment processes through digital construction principles: efficient collection of baseline data, high-detail design, classification of construction information, exchange of generated data between construction actors, etc. This renovation method also has the advantages of standardised production: ensuring greater accuracy, higher quality, less sensitive to the qualifications of the workers involved in the construction sub-tasks. Additionally, it reduces the duration of the construction work on site: less inconvenience for the occupants and lower labour costs. All these factors should lead to a faster, more efficient, and cost-effective building renovation process.
The second objective examines the feasibility of using plant-based organic materials for renovation, which have a neutral or lower climate impact compared to traditional materials. By sourcing these materialls locally, the carbon footprint of the construction process can be further reduced, particularly in terms of transportation emissions.
Figure 2: Installation of a wall insulation panel on the façade of a multi-apartment building in Estonia.
Panel renovation is a building envelope insulation technology in which the existing envelope is insulated by attaching a factory-built box-shaped panel that meets essential building requirements such as thermal performance, mechanical stability, and fire safety. The key element of this technology is a factory-built wall and/or roof panel, tailored to the individual dimensions of the building. These panels typically consist of a panel frame, thermal filler, exterior finishing, a fixing system, and other layers necessary to meet the essential requirements of the building. Wall panels are usually manufactured by factory-fitting the required window sizes. In some cases, panel renovation allows for increasing window area without changing the window width but in this case the renovation would also entail major changes inside the building. Panel technology also shifts a portion of the traditional on-site construction work to the factory, reducing labour requirements on-site and accelerating project completion.
Pilot projects and demonstrations
Panel insulation technology has already been tested in several EU countries through successful pilot projects. As most of these projects have received support from the European Union and other funding sources, visual material is available to the public to observe panel renovation processes both at the manufacturing facility and on-site during installation. Visual materials documenting these processes are available online (Note: the brand names of manufacturers featured in these materials are examples and do not represent an exclusive or recommended solution by the authors of this text):
The pilot projects show that panel renovation technology can be used both for the whole building (walls and roof) and for insulating only certain parts (more often walls). Also, in many cases, the insulation panel serves not only as a component to insulate the envelope but in some cases, engineering systems (ducts, electrical cables, small appliances) can be integrated into the panel.
Panel insulation is particularly recommended for buildings with simple geometric shapes and massive structures, such as reinforced concrete and masonry buildings. In certain cases, panel technology can be combined with traditional insulation methods, such as rendered or ventilated façade systems, to achieve optimal results.
Wall insulation panel
The components of the wall insulation panel must be selected so that the panel, as manufactured in the factory and installed in the building, complies with the essential requirements of the building, but may vary slightly depending on the manufacturer. Based on the experience of EU pilot projects, the main components of the wall insulation panel are as follows (Figure 3):
An intermediate layer of soft insulation material, with a thickness ranging from 0 to 8 cm, is installed to fill voids caused by irregularities in the load-bearing structure. The use of non-combustible insulation materials in this layer shall improve the fire resistance of the entire product. The thickness of this layer may vary according to the fixing solutions applied by the panel manufacturer and shall be specified in the manufacturer's recommendations for the particular panel.
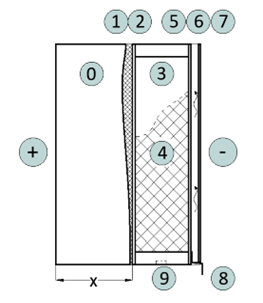
Figure 3: Main components of the insulating wall panel - wall section (0 - existing wall)
Particle board or similar material forming the 'box' wall of the panel. This layer provides rigidity to the panel and keeps the thermal filling in its designated position. The thickness should be between 10 and 12 mm.
Panel frame and internal frame, between which the insulating material is inserted. The panel frames and the frame provide mechanical rigidity to the panel, the other layers of the panel are attached to the frame, and the inserts are attached to the frame for installation and transport of the panel; Depending on the panel type, the frame may also accommodate windows and doors. Key requirements for this layer include dimensional stability, durability, mechanical strength, lightness, and good thermal performance. The width of the frames depends on the panel’s thermal performance requirements. The internal panel frame consists of struts spaced at 600 mm intervals, with a thickness of ≥5 cm. Frames may be constructed from calibrated sawn timber, glulam, plywood, plywood veneer, or other structural materials that provide adequate mechanical and performance properties.
Insulating material is inserted between the panel frame, the inner frame and the inner and outer walls. This filler material can be sheet-based or loose insulation and must comply with thermal, fire, and performance standards.
Windward-resistant gypsum board, forming the outer wall of the panel 'box', enhances thermal and fire performance. Thickness: 9,5-15 mm.
Façade frame, designed to create a ventilated air layer and support cladding installation. It consists of vertical struts with a thickness of 20-30 mm, and density varies based on the cladding’s fixing requirements.
Sheeting or cladding, made from materials such as wood, wood composites, fibre cement, profiled metal, and various plastics. Ceramic and stone cladding materials are not recommended due to their high weight.
Fire dampers, metal profiles that partially separate ventilation air layers between panels. Their use depends on the manufacturer’s panel construction approach.
Inserts and additional system elements, including wall mounting brackets and support beams.
Design considerations for insulation panels
When designing the layout of the insulation panels, it is important to take into account the deformation joints (if any) in the substrate to be renovated, and to ensure that deformation joints between insulation panels align accordingly. Additionally, panel design is more influenced by transport logistics than by production constraints.
For roof, basement, and underground foundation insulation, traditional techniques should be used, incorporating moisture-resistant insulation materials suitable for these applications. Conventional insulation for plinths and foundations does not require scaffolding, unlike panel insulation technology. When insulating partitions to unheated basements, the insulation strategy should be integrated with other insulation solutions. However, traditional insulation methods remain the most suitable for these structures.
Panel insulation and BIM
BIM technologies are gradually replacing the traditional processes of creating, managing and utilising information about the built environment. More digital data is generated at various stages of a building’s lifecycle, offering significant potential when made machine-readable. As the volume and range of digital data in construction projects grow, the challenge of integrating and organising this data increases. The above statements highlight the importance of standardising and structuring data models, as well as the role of classification in advancing digitisation. Table 1 presents a classification example of the wall insulating panel according to Lithuanian National Construction Classification framework, categorised by functional systems (ontology tag <L>F), technical systems (ontology tag <L>T), and components (ontology tag <L>C).
Table 1. Classification of the wall insulating panel components according to Lithuanian National Construction Classification framework
Important considerations
Before insulating a building with panels, a thorough assessment of its condition is essential. This includes an analysis of its thermal performance, airtightness, mechanical properties, and geometry. It is also important to assess the building environment when planning a panel renovation, as this type of insulation is usually carried out without scaffolding, using vehicles that require a larger clear space around the building for their passage. Adjacent plots of land should also be taken into account when assessing the building environment, as they can be temporarily used for panel insulation without the owners' objections. If the mechanical or geometric characteristics of the building are found to be unfavourable for panel renovation, it may be economically irrational to implement panel insulation technology, even though it is technically feasible.
Panel renovation achieves energy savings similar to traditional insulation technologies. However, since part of the construction work is conducted in a factory, panel technology has the potential to deliver superior economic and environmental performance. When selecting and evaluating panel design from an environmental perspective—specifically in terms of global warming potential (GWP)—the primary considerations should be the properties of the panel frame and insulation material, as these are the most prevalent components in the panel.
The requirements for insulating panels can be realised through a wide variety of solutions for the design and installation of the panel itself, but the safety of the chosen design must be based on European or national technical assessments. Differences in panel frame material and geometry, filling types, panel fixing and joining technologies, additional fire safety solutions, etc., may cause different results, so the exact solutions for the renovation of the building have to be evaluated and decided by the designers, by analysing the integrated products offered by the different manufacturers and by referring to the manufacturers' technical catalogues or other technical information. For maximum efficiency, panel technology can be combined with conventional renovation methods, exploiting the advantages of each technology. It is also appropriate to gradually start integrating engineering system components (ventilation units, ducts, etc.) into panel structures as the market gains more experience, as the integration of these components, especially in multi-storey buildings, also entails additional challenges in terms of fire safety and additional maintenance work.
Conclusion
Insulating old buildings with panels is one of the technologies for improving the energy efficiency of buildings. Due to its specific nature, panel insulation is used for more complex renovations, such as including replacement of all the windows in a building, reconstructing the balconies and changing the roof type. Panel insulation technology enhances a building’s energy efficiency and, combined with integrated solutions, brings a new quality to an old building. Building owners must be objectively informed about panel renovation options to select the optimal solution that aligns with their expectations, and that the tasks of all participants in the renovation process are shaped by this solution.
References
1 The renovation wave in Europe: greening buildings, creating jobs and improving lives
2 Renovation of apartment buildings with prefabricated modular panels. Kalle Kuusk, Peep Pihelo, and Targo Kalamees. E3S Web of Conferences 111, 03023 (2019) CLIMA 2019.