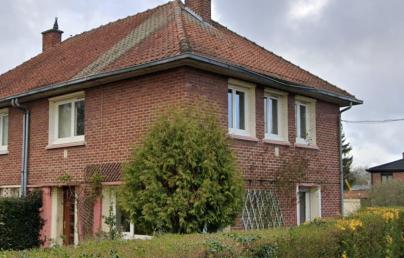
Energy rehabilitation of a social housing façade
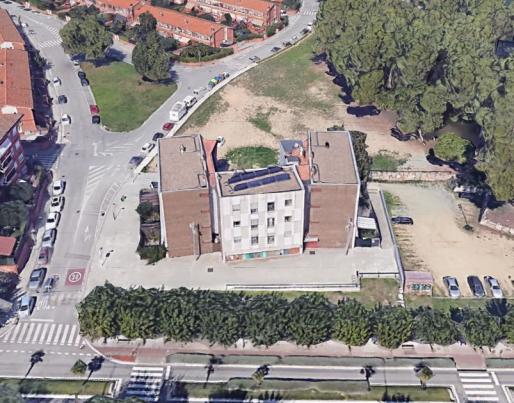
Energy rehabilitation of a social housing façade
This case study presents the energy rehabilitation of a facade of a social housing building located in Catalonia through the installation of an innovative, prefabricated, and modular facade system that integrates active and passive technologies and circular economy principles.
Main facts:
- Project type: Renovation of the thermal envelope and incorporation of photovoltaic panels
- Building type: Multifamily social housing
- Building location: Block A of the complex Ronda Arraona 29-31, Sant Quirze del Vallès (25 km from Barcelona, Catalonia)
- Floors/Height: Ground floor + 3
- Construction year: 2003
- Climate zone: C2 (Mediterranean climate zone, with warm and dry summers and mild, wet winters)
- Built-up area: 403.28 m2
- Usable area: 347.4 m2
- Construction/refurbishment cost: 178,776.64 €
- Project date: May 2021
- Works start date: 15th March 2022
- Works end date: 25th May 2022
- Duration of the works: approximately 2.5 months
Background
The residential property, built in 2003, is owned by INCASÒL but managed by Agència de l'Habitatge de Catalunya (AHC). It is a U-shaped public social housing consisting of 3 independent rectangular blocks with a central patio open to the north and a total of 30 homes plus 1 commercial premises. All dwellings are intended for social uses. Therefore, the income level of their tenants is low.
Building state before the renovation
It is a building that presented a lot of problems of condensation, humidity, and thermal comfort (existence of many thermal bridges and windows with very low permeability). Both humidity problems and poor thermal comfort were related to some damage detected in the external cladding of the façades of all 3 blocks.
Moreover, the building was built previously to the current Spanish technical code (CTE), which sets the minimum requirements to comply in the construction sector. This means that its energy demand was very high, rated G in the energy performance certificate. However, there was a solar thermal installation in the rooftop of block A (18.6 m2), which covered up to the 60% of the domestic hot water demand.
With the aim of improving the dwellings’ habitability and increasing their energy efficiency, AHC agreed with the building owner to carry out a renovation action.
The first step was to correctly diagnose the existing pathologies of the building. Specialist technicians from AHC carried out an exhaustive study to determine the existing deficiencies to solve and evaluate the best options to achieve the improvement of the dwellings, considering social, environmental, and economic factors. Users’ energy consumption data (by monitoring electricity bills and conducting surveys and inventories) were used, among others, to find out in detail the energy and social problems of the building.
With the aim of improving the dwellings habitability and increasing their energy efficiency, AHC proposed to the building owner to apply the innovative solution of the prefabricated multifunctional façade funded within the framework of the European Commission innovation programme H2020-768735 PLUG-N-HARVEST.
Evolution of the rehabilitation project
All PLUG-N-HARVEST renovation actions were focused on Block A, which has a ground floor with 1 commercial premises and 3 floors with 2 apartments each one. At the initial state the walls and roofs were insulated while the windows were double-glazed. The main façade is oriented to the south while the service façade, where the access to the apartments is located, faces north.
The main action carried out was the implementation of an innovative ADBE (Adaptable/Dynamic Building Envelopes) façade system designed by the PLUG-N-HARVEST project, which integrates plug and play concepts, as well as modular architecture and circular economy.
The new façade system, adaptable and modular, is made up of elements that can be easily disassembled and exchanged if necessary. It incorporates both passive and active elements. The passive ones perform the function of providing the building with a new cladding, increasing the isolation layer in the opaque part (wall) and improving the thermal characteristics of the translucent parts (windows and glass), as well as improving the solar protection by means of new automatic shutters, while reducing the energy demand of the building. The active elements are façade modules including PV panels as cladding, capable of generating electricity. In this way the building can use energy more efficiently and, in addition, renewable energy is generated and distributed on site.
The ADBE system was implemented on the southern façade, which was the façade that best suited in terms of surface and orientation for the placement of the industrialized solution.
Specifically, the innovative façade, which covers an area of 101 m2 of the 130 m2 of the existing façade, is based on a prefabricated aluminium structure that integrates the window carpentry and the shading elements of the translucent part, as well as photovoltaic modules to produce electricity. The innovation of the system lies in the design of a new aluminium profile able to integrate all the solutions adopted for the studied building. Economic (low manufacturing and installation costs, and almost zero operating and maintenance costs) as well as circular economy criteria (recyclable solutions and use of non-toxic materials) were taken into account both in the design and in the choice of materials.
An architectural adaptation of the modules and systems (plug and play and ADBE) to the building characteristics was required for the implementation of the PLUG-N-HARVEST façade system.
Once the profile of the ADBE façade was designed, a mold was created for its manufacture. After some difficulties, the profile was successfully obtained, and then the façade panels and the prototype were assembled.
At the same time, the solution was evaluated by an independent laboratory in order to certify its performance and guarantee its optimal quality, as well as compliance with current regulations and that the maturity degree of the technology developed was suitable for its implementation in a building in use.
The innovative construction and technological PLUG-N-HARVEST solution meets the following needs:
- It is modular and allows to reduce construction time (thereby reducing users inconvenience) and the manufacture, installation, and operation costs (in case of being implemented on a larger scale) compared to a conventional solution with renewable energies adaptation.
- It allows the transformation of conventional static facades to more active ones with the integration of renewable energy production elements for a greater thermal comfort, being able to adapt dynamically to the available energy assets.
- It guarantees its replicability.
- It comprises a high rate of circularity, both in design and in materials. For this reason, it includes all the design guides and indications regarding circularity proposed within the framework of the PLUG-N-HARVEST project.
Materials
The aim of the rehabilitation works carried out was to increase the degree of circularity and energy efficiency of the building. The works consisted of removing the deteriorated ventilated facade, increasing the thermal insulation of it (with the incorporation of passive solutions based on circular economy principles such as the use of low environmental impact insulations) and the installation of photovoltaic energy systems.
The implemented façade is made up of 21 ADBE modules (total area of 101 m2), of which 9 have photovoltaic panels of different sizes, 6 are double modules with window-opaque elements and the remaining 6 are triple modules with opaque-window-opaque elements. The ADBE modules are made up of assembled aluminium panels that include an internal thermal insulation layer (rock wool with a thickness of 10 cm) to reduce heat losses and outdoor photovoltaic panels of amorphous silicon to generate electricity (with an installed photovoltaic peak power of 6.22 kWp). On the other hand, the modules with window integrate automatic metal shutters and double-pane windows with internal argon gas chamber and aluminium frame with thermal break.
The resulting new industrialized façade has a thermal transmittance of 0.27 W/m2K (opaque modules) and 1.18 W/m2K (windows). The values are lower than the maximum U required by the Basic Energy Saving document of the Spanish Technical Building Code (0.49 W/m2K and 2.1 W/m2K, respectively).
The energy generated will be distributed equitably to all the dwellings in the building in the modality of collective self-consumption with compensation for surpluses.