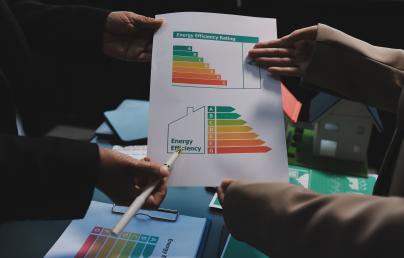
Sustainable retrofitting of buildings through the lens of an industrialised approach

Sustainable retrofitting of buildings through the lens of an industrialised approach
Traditional renovation methods often prove slow and disruptive. One effective approach is industrialised renovation, which leverages methods such as automation, digitalisation, standardisation, mass production, and prefabrication to reduce emissions, ensure higher precision, cut costs, and accelerate onsite assembly.
Renovation case studies like Energiesprong and the European INFINITE project highlight the potential of this approach. Additionally, European legislation actively supports deep renovation, fostering an environment conducive to industrialised renovation.
However, regulatory, financial, and cultural barriers persist, necessitating targeted policies and workforce upskilling to drive broader adoption. This article explores the benefits, challenges, and market potential of off-site construction for energy-efficient building renovations, highlighting examples and policy support across Europe.
(Note: Opinions in the articles are of the authors only and do not necessarily reflect the opinion of the EU)
Introduction
Key figures from the Energy Performance of Buildings Directive (EPBD) underscore the urgency of investing in building renovation:
Buildings account for 40% of energy consumption in the EU.
Over one-third of EU’s energy-related greenhouse gas emissions originate from buildings.
More than 85% of buildings in the EU were constructed before 2000, with 75% of those exhibiting poor energy performance.
While constructing energy-efficient, zero-emission buildings is critical—especially under the EPBD Recast mandate for non-residential buildings by 2030—the urgency of renovating existing buildings cannot be overstated. Ignoring these would jeopardise climate neutrality goals. Sustainable renovation also plays a vital role in addressing energy poverty. Improved energy efficiency lowers utility costs, enhances affordability, and improves living conditions.
This article examines sustainable renovation through an industrialised lens, presenting case studies and best practices to illustrate its viability, carrying forward a discussion that was initiated in a previous Overview Article.
Industrialisation as an enhancer of building refurbishment
The concept of industrialisation in the construction industry can vary depending on the context and country. However, its defining feature is a shift from traditional on-site construction methods to industrialised off-site production. This transition incorporates elements such as automation, digitalisation, standardisation, mass production and prefabrication.
Industrialised renovation, which is cost-competitive with traditional methods if a comparative Life Cycle Costing (LCC) is applied, offers significant advantages in terms of CO₂ savings and implementation speed.
Off-site production technologies are expected to reduce construction waste by 10–15%, lower costs, and accelerate timelines, both for new builds and renovations.
A 2019 report by McKinsey, which focuses on new builds, provides further insights on the subject. The projects analysed that adopted a modular approach demonstrated a 20-50% acceleration in project timelines (more recent estimates broaden the range to 60%). Moreover, according to the same report, scaling this approach to an economy of scale could result in cost savings of up to 20%.
The latter data, although referring to new buildings, provide an important element for understanding some of the advantages of the off-site approach, even in the case of renovation.
Success stories from the field
To understand how this process unfolds in practice, it can be helpful to examine some examples of retrofitting.
A leading example in Europe of off-site prefabrication is Energiesprong, a retrofit model originating in the Netherlands, which aims to be both economically sustainable and scalable on a large scale. The Energiesprong model is currently being replicated and upscaled in other countries, including France, Germany or Italy, including with the support of EU funds. Market development teams work with policy makers and financial institutions to create an enabling framework that supports large-scale building retrofits. They coordinate housing associations, construction companies and technology manufacturers to launch pilot projects and scale up to collective retrofits.
One of the notable success stories is the intervention on Via Russoli in Milan, where an outdated residential complex required extensive refurbishment to meet modern energy performance standards. The results, achieved within a short construction timeframe, are impressive: from the use of bio-based façades for energy retrofitting -produced off-site and installed without scaffolding- to the implementation of a new photovoltaic system. These measures resulted in a significant improvement in the building's energy performance. Special attention was also given to renovating the common areas, which were transformed into green, lush spaces to enhance the social experience.
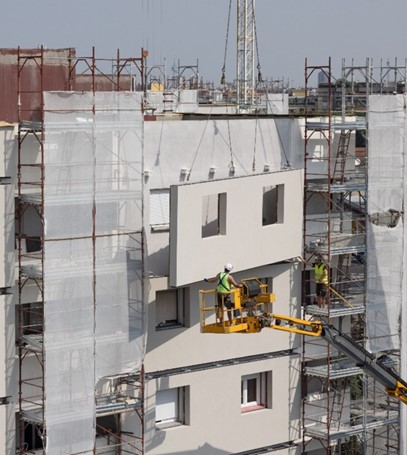
Figure 1. The refurbishment of the Via Russoli complex. Credits: Energiesprong it.
Another example of a demo-case that adopts an industrialised approach to building renovation comes from the Horizon 2020 project, INFINITE. This project focuses on renovating building envelopes using a modular and industrialised approach. With several ongoing demonstration projects, INFINITE offers cost-effective and innovative solutions for deep building renovation.
At a national scale, one notable example is a Slovenian case, which is nearing completion. The project includes, among other features, the installation of Building-Integrated Photovoltaic (BIPV) panels —photovoltaic panels integrated into prefabricated wooden structures that can be mounted on the building’s facades or roof. These panels are available in various colours, ensuring that aesthetics is not compromised. Additionally, the project integrates a distribution system for ventilation and water supply, which is heated by heat pumps and used for both heating and cooling. This system is installed in prefabricated modules attached to the building façade. Modules with green cladding are also applied to both the façade and roof. The project is proving to be a success, with several goals achieved, including testing the mock-up of the BIPV façade on the actual building and installing timber-based façades in just minutes.
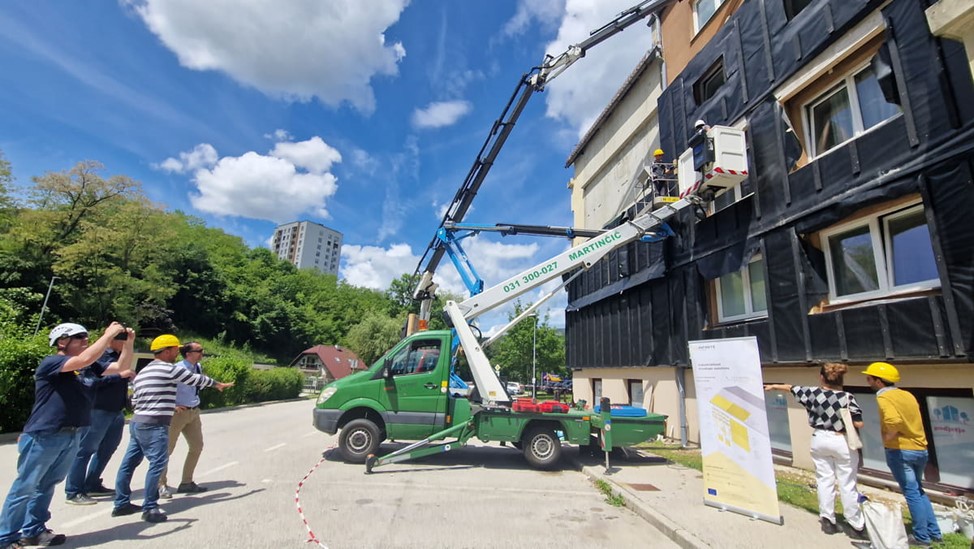
Figure 2. Installing timber-based façades at the Slovenian demo-case. Credits: INFINITE.
Current challenges
A recent report by the High-Level Construction Forum (HLCF) gives insights into the current state of off-site industrialised construction techniques in the EU. Some countries have made significant progress in this area, particularly the Nordic countries. For example, Sweden constructs more than 90% of its single-family homes using prefabrication. In contrast, this figure drops to just 1% in Spain.
In other Member States, such as Germany, Austria, and Switzerland, the use of modular timber elements is increasing. However, off-site construction remains a niche phenomenon in most other European countries. This is also true for off-site renovation, for which quantitative data on adoption is scarce. Among the leading examples, the Netherlands stands out, where the Energiesprong network aims to refurbish 111,000 homes into net-zero energy buildings. Overall, the adoption of off-site renovation follows a similar pattern to off-site construction, with higher uptake in certain regions but remaining a niche practice in most of Europe.
Hence, what are the barriers to wider adoption of off-site methods?
Skills gap: the construction sector faces a workforce shortage, with many workers lacking training in off-site techniques.
Regulatory disparities: while EU legislation promotes modern renovation, national regulations vary, creating bureaucratic obstacles.
Financial constraints: off-site production requires substantial upfront investment. Though cost-competitive at scale, smaller projects struggle with economic feasibility.
Cultural resistance: many stakeholders remain skeptical about the durability and quality of modular construction.
Overcoming these challenges requires workforce upskilling, policy harmonisation, increased market adoption, and knowledge-sharing on best practices.
EU policy framework
Article 3 of the EPBD requires each EU Member State to submit a national renovation plan every five years, following Annex II guidelines. These plans must outline, amongst other things, policies and measures for the promotion of modular and industrialised solutions for construction and building renovation, including objectives, funding sources, and implementation strategies.
The Directive also promotes deep renovation, which significantly enhances a building's energy efficiency and performance.
The term ‘industrialised renovation’ appears in this context, though it is frequently linked with deep renovation due to its transformative approach. In fact, the Directive defines deep renovation as ‘a renovation that transforms buildings into zero-emission buildings but, as a first step, as a renovation that transforms buildings into nearly zero-energy buildings.’
Deep renovation is therefore crucial for achieving the decarbonisation goals outlined in the Directive. Member States are encouraged to support deep renovation measures through financial, fiscal, administrative, and technical means (Article 17).
Staged deep renovation, introduced to mitigate financial and logistical barriers, allows incremental improvements while maintaining cost-effectiveness. Additionally, renovation passports guide property owners through the process, ensuring effective implementation.
The Construction Product Regulation, which came into force on 7 January 2024, further facilitates industrialised techniques by simplifying regulatory requirements and encouraging modular, prefabricated solutions.
European and national projects
The following is a selection of projects related to industrialised renovation at both European and national levels and does not claim to be exhaustive.
LifeGigaRegioFactory Logo
LIFE21-CET-BUILDRENO-LifeGigaRegioFactory, Start date: 01/11/2022 - End date: 31/10/2025
The Life Giga Regio Factory project aims to renovate 1 million European homes to zero-energy levels by 2030. It involves a multi-country consortium focused on industrialised retrofits, open-source tools, and scaling solutions for mass home renovations.
COSME RENO Logo
LIFE22-CET-COSME RENO, Start date: 02/10/2023 - End date: 01/10/2026
The project aims to develop better cooperation tools and create a Small and Medium-sized Enterprises SME tooling academy, activate shared investment and partnership capacities for SMEs involved in deep energy retrofit, and leverage innovative financing and warranty mechanisms.
BARRIO Logo
LIFE23-CET-BARRIO, Start date: 01/10/2024 - End date: 30/09/2027
BARRIO integrates neighbourhood-level demand aggregation, innovative business models, and industrialised prefabricated solutions to streamline deep renovations, while the Defragmentation Multidisciplinary Toolkit clusters buildings and prioritises stakeholder needs for large-scale decarbonisation efforts.
LIFE-Reno-Tides Logo
LIFE23-CET-LIFE-Reno-Tides, Start date: 01/10/2024 - End date: 01/10/2027
The project aims to organise smartly designed 3 staged deep energy retrofits with multiple building owners such as social housing organisations.
Horizon Europe
INPERSO Logo
INPERSO, Start date 01/07/2022 - End date 30/06/2026
INPERSO is a deep renovation program focusing on sustainable, efficient, and affordable building renovation using prefabrication, 3D printing, and digital technologies. It aims to reduce costs, improve energy performance, and promote green financing.
InCUBE Logo
InCUBE, Start date: 01/07/2022 - End date: 30/06/2026
InCUBE unites 23 partners across 7 EU countries to innovate building renovation through industrialisation, self-RES technologies, digitalisation, and new business models, aiming for cost reductions, energy savings, and improved sustainability.
REHOUSE Logo
REHOUSE, Start date 01/10/2022 - End date 30/09/2026
REHOUSE aims to develop 8 innovative renovation packages for deep renovations, focusing on sustainability, affordability, and flexibility. It promotes circularity, prefabrication, and aesthetic preservation, tested across EU locations to boost scalability.
REN+HOMES Logo
REN+HOMES, Start date: 01/06/2023 - End date: 30/11/2026
REN+HOMES tackles energy and emissions issues by developing 23 sustainable solutions, including industrialised and prefabricated hardware like recycled material panels and BIPV facades, alongside software and methodologies for energy efficiency.
Horizon 2020
INFINITE Logo
INFINITE, Start date: 01/11/2020 - End date: 30/04/2025
The INFINITE project aims to decarbonise the EU building stock by promoting industrialised energy-efficient renovation technologies. It focuses on cost and time reduction, life-cycle sustainability, and stakeholder acceptance, enabling widespread adoption.
ENSNARE Logo
ENSNARE, Start date: 01/01/2021 - End date: 01/02/2025
The EU-funded ENSNARE project aims to enhance building envelope renovations through digitalisation and industrialised mesh systems, validating its solutions with three pilot projects linked to digital twins of renovated buildings.
Other European projects
BuildOffsiteEU Logo
BuildOffsiteEU, Start date: 01/12/2022 - End date: 01/12/2024
BuildOffsiteEU enhances vocational training in industrialised construction to meet labour market needs, addressing key competencies, environmental challenges, workforce transition, sector image, and employability while distinguishing construction systems and engaging stakeholders.
National projects
oPENLab Logo
Estonia – The Horizon 2020 oPEN LAB project in Tartu, advances industrialised renovation using prefabrication for high-rise buildings. TalTech leads research, with national funding supporting five-story renovations. A 9-story project is entering design and implementation soon.
BUILD UP Skills Logo
Lithuania - The BUILD UP Skills initiative aims to upskill building professionals in Lithuania, fostering stakeholder collaboration to meet 2030 energy goals. It focuses on NZEBs, industrialised renovation, and sustainable roadmap implementation.
Greece – The LIFE funded BUS-REGRoUP revitalises Greece’s National Qualifications Platform by expanding stakeholder involvement, addressing blue- and white-collar skill needs, supporting industrialised renovation, and updating roadmaps for clean energy and NZEB transitions.
Spain - ALIGRA is a prefabricated timber module system for renovating and expanding housing. Selected in 2023, a prototype in Barcelona tests its water and energy efficiency as an open-source, patent-free solution.
Conclusion
Industrialised renovation presents a promising pathway for achieving energy efficiency and sustainability in Europe’s building sector. While successful initiatives such as Energiesprong and the INFINITE project highlight the potential of this approach, broader adoption hinges on addressing skills shortages, regulatory misalignment, and financial constraints.
The EU’s legislative support, coupled with increasing market investments, offers a strong foundation for expanding industrialised retrofitting.
National information for this article collected by BUILD UP Ambassadors Dorin Beu (Romania), Merit Tatar (Estonia) and Cristina J. Pulido (Spain)
We encourage readers to visit our portal to stay informed and further explore these topics.